What can you do to help save vast amounts of water? Take a look at the mechanical seals and gland packing on the rotating equipment in your factories and plants.
We are all told day after day, save money, save energy, save the environment. From person to person and business to business, we are all looking to achieve the best savings by whatever means possible.
Here’s another one – save water!
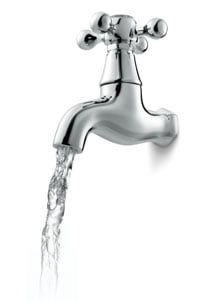
So water, you might think it’s plentiful when you look on a map and see the large blue areas of water across the world. It appears to be a seemingly endless resource… However did you know that just 0.6% of the world’s water is actually suitable for industrial use and human consumption? Neither did I, and the sooner more of us in manufacturing realise this, the more water we can all save. Instead of spending money like water, let’s spend water like money.
So now you also know, but what can you do about it? Well you could pass this message on… but you could also take some decisive action.
What can you do to help save these vast amounts of water?
Take a look at the mechanical seals and gland packing on the rotating equipment in your factories and plants.
If you have gland packing for sealing your pumps, you could be using somewhere in the region of 6.3 million litres (1.6 million gallons) of water a year! Similarly, if you are using a single mechanical seal and using water as opposed to the process fluid for keeping seal faces cool and clean, then you may also be using similar amounts of flush water.
If the process fluid isn’t suitable for cooling or cleaning, consider using a double mechanical seal with a seal support system. It could really be as simple as that. Although each application is different, there are very few processes that really need to use 23 million litres (6 million US gallons) per year… and that is per seal. A dual mechanical seal and system could reduce water consumption by up to 99.9%.
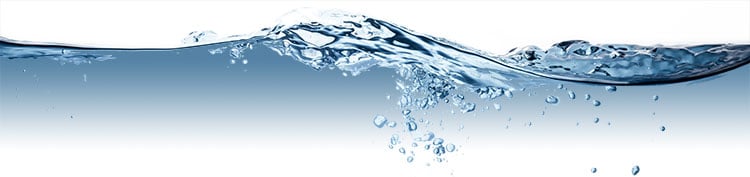
If the water saving alone isn’t enough to convince you, have you thought about where all that water goes? Well it’ll be no surprise that most of it goes down the drain (and you pay again for the water to be treated prior to disposal), but also some may end up in your product. This might be acceptable but if not, then additional processes have to be carried out in order to remove it. Typically this would be done through heating and evaporating off the water, adding furthermore to your energy bill.
By changing your sealing methods, you are also highly likely to improve the reliability of your pump, reducing the likelihood of breakdowns and downtime for repair, which lead to an increase in maintenance costs. Not to mention the loss of production. The pump bearings are typically in close proximity to the seal too and if using leaky gland packing, it is highly likely that you will have to endure failures and have to deal with downtime whilst a repair takes place. This is where you may consider bearing protection, something like the LabTecta®66 that seals to IP66 would be a great choice. More than half of all bearing failures are down to the contamination in the bearing oil. By upgrading your lip seals to a bearing protector, you can effectively eliminate any contamination increasing uptime and saving on the frequent repairs and spare parts needed to keep operational.
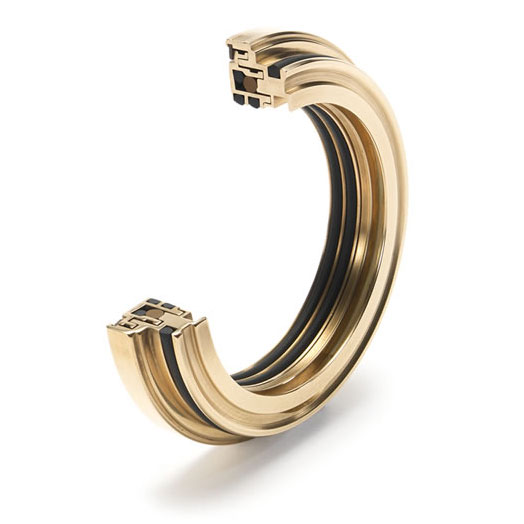
You may also wish to consider the cleaning bill if you are using sealing methods such as gland packing, which naturally leak far more than a mechanical seal. If it’s just plain water you are flushing or pumping through the process, it may not be such an issue but if it’s a thick sticky substance then the clean up costs may increase somewhat.
So when we look at saving water in our manufacturing facilities, there are actually far more benefits than a reduced water rates bill. In summary, to save water and in turn energy, maintenance and clean up costs, as well as improvement of reliability. We urge you to assess whether you have the right sealing technology on your equipment. It could prevent you being sold down the river.

CASE STUDY: 4.5 Billion litres of water saved in 6 years
International packaging and paper group Mondi installed AESSEAL® water management systems at its Richards Bay mill, helping to conserve scarce water resources in northern KwaZulu Natal. AESSEAL® installed type-SW2 and SW3 water management systems that will use recycled water to cool, lubricate and flush mechanical seals in the Richards Bay plant. The new AESSEAL® systems will help save Mondi over 4.5 Billion litres of water and £568,890 within 6 years.
Act now to save our water future
As recently reported by the UK Environment Agency, it is anticipated that at the current rate of population growth, water use and leakage, demand for water will outstrip supply by 2050.
Reports convey much around our own individual consumption and how we can make small changes to help conserve water. However there is a lot of waste within manufacturing facilities and this is where we can help.
A pump can consume on average around 6 litres per minute and would typically just go down the drain. That is just one pump. Imagine if a plant or factory has 10, 20 or even 100 pumps… all that water is wasted and with the right technology in place, this can be eliminated with a suitable seal and seal support system in place.
6 litres per minute per pump can be reduced to less than a cup a month. The savings are huge! With this kind of system in place, not only will a business help to save an extraordinary amount of water, they will also save any associated cost of effluent clean up. In some cases, the excess water can also make its way into the process which can also lead to further treatment of the process to remove that extra water. Methods such as evaporation and reheating leads an increase in energy use.
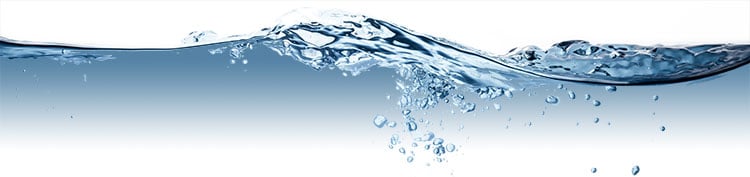
Save billions of litres of water through intuitive use of seal support systems
At AESSEAL® we often write about water savings as we are a solution led business but we have a genuine passion to drive a behavioural change to help protect our environment and help save our resources. It is all our responsibility to protect and preserve to pass on to the next generation and they to the next one and so on…
The important thing to note is that it is not too late! With the right solutions in place and in partnership with other manufacturing businesses we can collectively save billions of litres of water.
Let’s not sit back and watch it happen. Take action today.
Contact us to find out how we can also help your business save billions of litres of water.